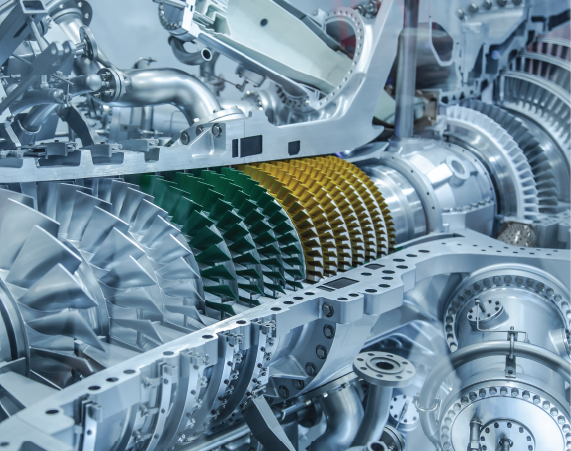
Gas Turbine Performance: Boost Gas Turbine Efficiency & Optimization
When you look at today’s energy facilities, one thing stands out—how well the machines convert fuel into electricity. This topic has sparked a lot of discussion among engineers and plant managers, especially when it comes to gas turbines. Over the years, many have examined power plant efficiency from every angle, finding that gas turbines lead the way in performance improvements. In this article, we break down what drives efficiency in a gas power plant, share data and trends from trusted sources, and explain why your used, end-of-service, or broken gas turbine parts can find a new lease on life with Gas Turbine Spares.
What Does Power Plant Efficiency Mean?
At its core, power plant efficiency is all about comparing the energy in the fuel to the electricity produced. In simple terms, it is a measure of how much useful work comes from every unit of fuel. The U.S. Energy Information Administration explains that the ratio of energy output to energy input defines power plant efficiency. This means that every fraction of a percentage point in efficiency counts, especially when operating at a large scale.
Over the past century, people have tracked how different types of power plants—coal, nuclear, natural gas, and more—perform. Historical data, such as that compiled by Visualizing Energy, shows clear trends that point to a steady improvement in efficiency over time, particularly as gas turbine technology has advanced.
Gas Turbine Efficiency: The Basics
Gas turbines operate by drawing air in, compressing it, mixing it with fuel, and then igniting the mixture. The hot gases produced spin the turbine, generating electricity. The efficiency of a gas power plant depends on how effectively these processes turn fuel into usable electricity. More efficient turbines reduce fuel costs and lower emissions, making them a smart investment for plant operators.
Data from various sources, including insights from PCI Energy Solutions and Woodway Energy, show that natural gas plants have been improving steadily. They offer some of the highest efficiency ratings among fossil fuel-based plants, which means less fuel is wasted in the conversion process.
The Numbers Behind Efficiency
There’s plenty of evidence that gas turbines have come a long way in performance. Wikipedia provides a comprehensive look at power plant efficiency, breaking down how different designs and fuels affect overall output. More recent evaluations from the National Renewable Energy Laboratory’s ATB archive show that new turbine models consistently push efficiency records higher.
In discussions among science enthusiasts on forums like Reddit, many experts highlight that improvements in turbine design have led to more efficient fuel conversion. The conversion efficiency from fuel to electricity in modern gas power plants has reached levels that were once thought impossible.
Factors That Impact Gas Plant Efficiency
Several elements play a role in how well a gas power plant performs. Here are some of the most critical factors:
- Turbine Design: Advances in turbine blade materials and aerodynamic design have made it possible for turbines to operate at higher temperatures. These improvements allow the engines to extract more energy from the same amount of fuel.
- Fuel Quality: The type and quality of fuel used affect the combustion process. Cleaner fuels with fewer impurities ensure a smoother and more efficient burn.
- Maintenance Practices: Regular upkeep of turbine components, including cleaning and part replacement, is key. Well-maintained turbines operate closer to their peak efficiency, avoiding losses from wear or damage.
- Operating Conditions: External factors such as ambient temperature, humidity, and altitude also affect performance. Even small changes in operating conditions can shift the efficiency balance.
Each of these factors contributes to the overall picture of power plant efficiency, and keeping them in check is vital for plant operators aiming for top performance.
Common Issues in Gas Turbine Performance
Even the best-designed gas turbines can face challenges that reduce efficiency. Some issues that facility operators commonly encounter include:
- Wear and Tear: Over time, parts of the turbine experience fatigue, which can lower performance. Regular inspections and timely part replacements are necessary to maintain high efficiency.
- Fuel Variability: Changes in fuel supply or quality can impact the combustion process. Operators need to be aware of these shifts and adjust operations accordingly.
- Heat Loss: One of the largest components of energy loss in any power plant is heat. Efforts to recover and reuse waste heat can help improve overall efficiency.
- Environmental Factors: Shifts in ambient conditions can sometimes lead to slight drops in efficiency. Operators must monitor environmental conditions closely and adjust their operations as needed.
Each of these issues can have a noticeable effect on the overall efficiency of a gas power plant. Addressing them is not just about saving money—it’s about sustaining a reliable energy supply for communities and industries alike.
The Benefits of High Efficiency in Gas Turbines
Why should plant operators care so much about efficiency? The answer lies in the direct impact on operating costs and environmental performance. When a gas power plant operates efficiently:
- Fuel Costs Are Lower: Better efficiency means that less fuel is required to produce the same amount of electricity. This translates into savings on fuel expenses.
- Emissions Are Reduced: More efficient combustion leads to lower emissions of greenhouse gases and other pollutants. This is increasingly important in a world that is paying close attention to environmental impacts.
- Improved Reliability: Plants that maintain high efficiency typically experience fewer breakdowns. When turbines run smoothly, they are less likely to encounter unexpected issues that could lead to costly downtime.
- Competitive Advantage: For operators, a highly efficient gas power plant can provide an edge in a market where every percentage point of efficiency matters. Better performance can mean more consistent profits and a stronger position in the energy market.
Each of these benefits reinforces the importance of achieving high power plant efficiency. They also underline the value of taking action when components start to show signs of wear.
How Technology Has Driven Efficiency Improvements
Over the years, technology has steadily improved the efficiency of gas turbines. Newer models incorporate advanced materials and design techniques that allow for higher operating temperatures and pressures. This means that modern turbines are capable of producing more electricity from less fuel than their predecessors.
For example, research and commentary on sites like ASME’s blog about gas power plants have highlighted how improvements in turbine design have led to performance levels that far exceed those of older systems. Similarly, articles on Woodway Energy emphasize that even small improvements in the combustion process can result in significant efficiency gains.
This steady progress is also visible when comparing historical data. Visualizing Energy’s timeline on power plant efficiency since 1900 shows that while older technologies had modest performance, modern gas turbines are operating at much higher efficiency levels. This progress is not just a technical achievement; it has real-world benefits in terms of cost savings and reduced environmental impact.
The Role of Maintenance and Upgrades
A key factor in keeping gas turbines running at their best is regular maintenance and timely upgrades. Over time, even the most advanced turbines require attention. When components start to lose their effectiveness, efficiency drops and operational costs rise.
Plant operators often face the decision of whether to repair or replace parts that have reached the end of their service life. This is where Gas Turbine Spares come into play. Instead of letting used, end-of-service, or broken parts gather dust in storage, you have the opportunity to turn them into cash. By selling these parts to Gas Turbine Spares, you not only recoup some of your investment but also contribute to a more sustainable cycle in the industry.
Many facilities have discovered that keeping an eye on the condition of their turbines—and taking swift action when performance drops—can save significant money in the long run. With a focus on practical maintenance and upgrade strategies, operators can maintain high efficiency levels even as parts age.
Real-World Trends in Gas Plant Efficiency
Recent discussions and studies have reinforced the benefits of high gas turbine efficiency. Analysis from sources like PCI Energy Solutions and the Energy Information Administration illustrates that gas plants have been steadily increasing their performance metrics, thanks to both technological advancements and improved operational practices.
Experts have pointed out that as gas turbines get more efficient, the margin for error shrinks. This means that even small issues can have a larger impact on overall performance. Operators are learning to pay attention to details such as fuel mix, ambient conditions, and component wear. A well-run gas turbine facility can achieve impressive levels of efficiency, making it a popular choice in regions where fuel costs are high or environmental regulations are strict.
In fact, data from NREL’s ATB archive and discussions on Reddit have shown that continuous improvements in design and operation have led to a marked increase in the efficiency of a gas power plant over the past decade.
Addressing Concerns About Gas Turbine Performance
Some plant operators worry about the long-term performance of their turbines. Questions about part longevity, fuel consumption, and unexpected downtimes are common. It’s clear from numerous analyses that keeping gas turbines operating at high efficiency requires constant vigilance and action. When issues arise, they must be addressed promptly to avoid a drop in power plant efficiency.
Many of the concerns focus on the challenges of maintaining optimum operating conditions. A drop in the efficiency of a gas power plant can mean increased fuel costs and a higher risk of mechanical failure. Data and expert opinions suggest that routine checks and proactive replacement of worn components can mitigate these risks.
Plant managers who invest in monitoring equipment and regular maintenance protocols tend to see better overall performance. These practices help keep the combustion process as efficient as possible and avoid unnecessary heat losses—a major source of inefficiency in many plants.
Opportunities for Improvement and Innovation
While current gas turbine technology has made great strides, there is always room for improvement. Many industry players are working on new methods to optimize turbine operation, reduce fuel consumption, and lower emissions further. Emerging technologies in sensor monitoring and digital analytics are already making it easier to spot inefficiencies before they become serious problems.
Continuous improvement in operational practices is a key theme that recurs in discussions among industry experts. Studies from organizations like the International Energy Agency have shown that even small operational tweaks can lead to noticeable improvements in power plant efficiency.
Operators who embrace regular upgrades and modern maintenance practices are finding that their facilities not only operate more efficiently but also enjoy a longer service life. This proactive approach helps in managing the inevitable wear and tear that comes with daily operations.
How Gas Turbine Spares Fits Into the Picture
For many plant operators, managing a turbine fleet means making difficult decisions about what to repair, upgrade, or replace. When parts reach the end of their service life, they can either be discarded or sold for reuse. Gas Turbine Spares offers an attractive solution. By purchasing used, end-of-service, or broken gas turbine parts, they provide a valuable service to operators looking to maximize the value of their assets.
Selling these parts means that you can recover costs that might otherwise be lost. The spare parts, even if they are no longer fit for their original purpose, can be refurbished or used in secondary markets where they continue to serve a function. This not only supports the operational efficiency of your facility but also contributes to a more sustainable lifecycle for turbine components.
Many operators have found that working with Gas Turbine Spares provides both financial benefits and peace of mind. When a turbine is underperforming, rather than incurring high costs for new parts, selling your used components can offer immediate cash flow, which in turn can be reinvested into other areas of your operation. This practical approach helps maintain a strong focus on overall power plant efficiency.
Bringing It All Together
Gas turbines have proven themselves to be among the best options when it comes to efficient fuel conversion. The impressive numbers and consistent improvements across the industry confirm that high gas turbine efficiency isn’t just a hopeful idea—it’s a measurable reality. Power plant efficiency has improved steadily over the years, as shown by historical data and contemporary analyses alike.
When the efficiency of a gas power plant is at its peak, operating costs fall and profitability rises. Plant operators benefit from lower fuel consumption and reduced emissions. These benefits are directly tied to the careful management of turbine performance and maintenance. Even though every turbine faces challenges as it ages, proactive measures can ensure that performance remains high and that the overall gas plant efficiency stays competitive.
Investments in new technologies and continuous operational monitoring have paid off in the form of improved turbine performance. Trends and data from respected sources highlight that modern turbines achieve levels of efficiency that were unimaginable a few decades ago. In many cases, even a small improvement in efficiency can have a significant impact on a plant’s bottom line, making every improvement count.
Practical Steps to Maintain and Enhance Efficiency
For plant operators looking to keep their gas turbines in top condition, there are several actionable steps that can make a big difference:
- Regular Inspections: Consistent checks of turbine components help catch any signs of wear early. Regular monitoring of fuel quality, temperature, and pressure readings is key to ensuring that the combustion process remains stable.
- Timely Replacement of Parts: When a component shows signs of decline, replacing it quickly can prevent a drop in overall performance. It’s a common scenario: a small fault in a turbine can lead to a noticeable drop in the efficiency of a gas power plant. By addressing issues head-on, operators can keep their turbines running efficiently.
- Adopting Upgraded Components: Technology continues to improve. When newer, more efficient parts become available, consider incorporating them into your system. Even if the upgrade is incremental, the cumulative effect over time can lead to substantial savings.
- Data-Driven Decisions: Utilizing monitoring systems to track performance metrics can help you pinpoint where improvements are needed. With the right data, you can make informed decisions that keep the efficiency of a gas power plant at an optimal level.
- Collaborate with Trusted Partners: Sometimes, the best way to improve efficiency is to work with companies that specialize in gas turbine performance and spare parts. This is where Gas Turbine Spares makes a strong case for operators who want to convert old assets into a financial benefit.
Each of these steps supports the overall goal of achieving high power plant efficiency. By focusing on regular maintenance and embracing new components when available, plant managers can enjoy a more consistent and cost-effective operation.
Why Selling Your Used Turbine Parts Makes Sense
It might seem surprising, but there’s a hidden value in the parts that are no longer working at full capacity. Rather than letting these parts sit unused or be scrapped for little return, selling them to Gas Turbine Spares can be a smart move. Here’s why:
- Immediate Financial Return: When parts reach the end of their service, they still hold residual value. Selling these items can free up capital that might be better used to invest in new technology or maintain other parts of your facility.
- Reduced Storage Costs: Keeping outdated or broken components in storage can add up in terms of space and maintenance costs. By offloading these parts, you reduce clutter and create a more organized maintenance environment.
- Environmental Benefits: Reusing parts helps reduce waste. It means fewer components are disposed of, and the recycling of turbine parts can contribute to a more sustainable approach to managing resources.
- Improved Focus on Efficiency: Once you’ve cleared out the older, less effective parts, your maintenance teams can concentrate on ensuring that the remaining components operate at their best. This contributes directly to maintaining high gas plant efficiency and overall power plant performance.
Selling your used, end-of-service, or broken gas turbine parts isn’t just about turning unused assets into cash—it’s about maintaining a streamlined, efficient operation that supports the long-term success of your facility.
Real Success Stories and Industry Examples
Across the industry, many plant operators have embraced the idea of selling their surplus parts. Reports from reputable sources like Gevernova highlight instances where companies have successfully recouped funds from components that were once seen as liabilities. These success stories are not only inspiring—they also show that there is a healthy secondary market for gas turbine parts.
By participating in this market, operators gain flexibility. They are not locked into the high costs of new parts when a simple replacement can be sourced from a trusted partner. In turn, this practice helps maintain the overall efficiency of a gas power plant by ensuring that only the best-performing components remain in active service.
Many have shared experiences on industry forums and in trade publications about the benefits of a proactive maintenance strategy. These examples reinforce the idea that even when parts show signs of aging, there is still value to be extracted. In a market that rewards high efficiency, every component counts.
The Future of Gas Turbine Optimization
Looking ahead, the focus on efficiency is only set to increase. As the energy industry evolves, the pressure to get more out of every drop of fuel will remain high. Continuous improvements in turbine design and maintenance practices are expected to push the limits even further.
Several studies indicate that advancements in sensor technology and real-time monitoring systems will soon provide even more detailed insights into turbine performance. These developments will allow operators to catch small issues before they escalate, keeping the overall gas plant efficiency at peak levels.
New research and innovation continue to emerge, suggesting that the efficiency of a gas power plant can always be fine-tuned. This mindset of constant improvement is already reflected in many of the latest publications and reports. It’s a sign that the industry is committed to pushing performance boundaries, benefiting operators through reduced fuel consumption and lower operational costs.
Making the Decision: Sell Your Turbine Parts Today
Now that you have a clearer picture of what drives gas turbine efficiency and the impact it has on your facility, consider the next step. If your plant is in the process of upgrading or simply has surplus parts that are no longer meeting performance standards, there’s a practical solution at hand.
Gas Turbine Spares stands ready to purchase your used, end-of-service, or broken gas turbine parts. By selling these items, you unlock immediate financial benefits and contribute to a more sustainable operational model. It’s a straightforward decision that not only clears space and reduces storage costs but also reinforces the commitment to keeping your plant’s performance at its best.
By working with a partner who understands the intricate details of turbine performance, you can ensure that every component is valued and repurposed efficiently. This action supports overall power plant efficiency and helps you stay competitive in an industry where every percentage point matters.
Wrapping Up: Your Next Step
If you’re ready to take a practical step towards improved operational performance, consider the opportunity to sell your used turbine parts. In a market where efficiency is measured in every drop of fuel converted into electricity, no asset should be wasted. Selling surplus parts not only frees up resources but also allows you to invest in upgrades that can keep your gas power plant at the top of its game.
Remember, a well-run turbine operation means lower fuel costs, reduced emissions, and a better bottom line. The data and insights from respected sources all point to one conclusion—when your turbines perform at their best, your facility reaps the benefits in every aspect of the operation.
So, if you have components that are no longer running at their prime, reach out today. Contact Gas Turbine Spares to sell your used, end-of-service, or broken gas turbine parts. This step can help you recover funds, streamline operations, and keep your facility operating at peak efficiency. It’s a decision that aligns practical maintenance with long-term profitability.
Final Thoughts
Gas turbine efficiency continues to shape the future of power generation. With constant improvements in design, material, and maintenance practices, gas power plants are achieving levels of performance that translate directly into economic and environmental gains. From the detailed data provided by organizations like the U.S. Energy Information Administration and the insights shared on platforms like Wikipedia and ASME, one thing is clear: high efficiency is a cornerstone of modern energy production.
Every plant operator understands that the smallest improvement in efficiency can result in significant savings over time. Whether it’s through routine maintenance, the use of advanced turbine components, or the strategic sale of outdated parts, every effort contributes to a more stable and profitable operation.
Gas Turbine Spares is here to help you make the most of your assets. If your turbine parts are not performing at the level they once did, don’t let them sit idle. Convert them into a valuable asset by selling them to a partner who appreciates their worth.
Take action today and keep your focus on a future where every unit of fuel is used to its maximum potential. For any plant operator looking to improve overall efficiency and secure better returns on their assets, this is a step worth taking.
Contact Gas Turbine Spares now to sell your used, end-of-service, or broken gas turbine parts and see the difference that smart asset management can make. Your next step toward a more efficient operation is just one call or email away.
A Recap of Key Points
- What Is Power Plant Efficiency?
It is the measure of how much electricity is produced from a given amount of fuel. Every percentage point matters, especially in high-demand settings. - The Efficiency of a Gas Power Plant:
Gas turbines convert fuel into electricity with impressive efficiency, thanks to design improvements and better fuel management. These systems are leading the way in efficiency metrics. - Factors Affecting Gas Plant Efficiency:
Turbine design, fuel quality, maintenance, and operating conditions all play crucial roles. Even minor improvements can result in significant cost savings and reduced emissions. - Challenges and Opportunities:
Common issues such as wear, heat loss, and fuel variability can reduce efficiency. Addressing these issues through proactive maintenance and strategic upgrades is key. - The Value of Selling Used Parts:
Selling parts that are past their peak performance provides an immediate financial return, reduces storage costs, and supports a sustainable cycle in turbine maintenance. Gas Turbine Spares offers a smart solution for these challenges. - Looking Ahead:
With ongoing improvements in sensor technology and turbine design, gas turbine efficiency is expected to rise further. This progress benefits operators by reducing operational costs and increasing overall profitability.
Your Invitation to Act
Every plant operator faces the challenge of balancing cost, performance, and sustainability. High power plant efficiency is not a distant goal—it is achievable today with the right approach to maintenance and component management.
If you have turbine parts that no longer meet the demands of modern operations, remember that they still carry value. Instead of letting them become a financial burden, take advantage of the opportunity to turn them into cash. Gas Turbine Spares is ready to evaluate and purchase your used end-of-service, or broken gas turbine parts. This is a straightforward way to improve your facility’s efficiency and free up resources for future upgrades.
Get in touch with Gas Turbine Spares now. Transform idle assets into immediate returns and join the many operators who have already taken control of their turbine performance. Your facility’s efficiency, profitability, and sustainability depend on it.
I WANT TO SELL
Do you have any spare parts for gas turbines you want to sell? Please Inquire now through our online submission form or contact us via phone, to assess the value of your as-removed parts.