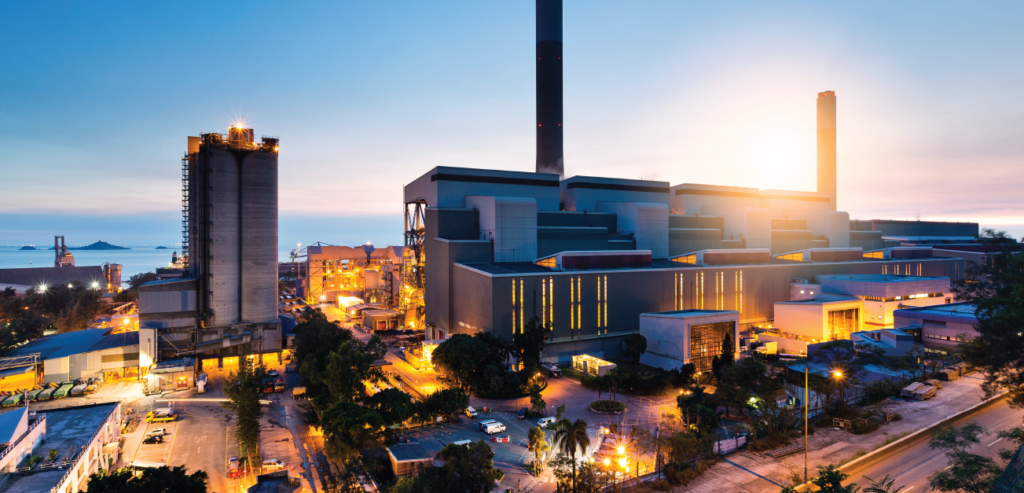
Life Cycle of Jet Engine Turbine Blades
1. Design and Material Selection
- Design Phase: The design of jet engine turbine blades is crucial as they must withstand extreme conditions. Engineers design blades to balance aerodynamic performance with structural integrity and thermal resistance.
- Material Selection: High-performance turbine blades are typically made from nickel-based superalloys, such as RENE N-6. These materials are chosen for their exceptional high-temperature strength, toughness, and corrosion resistance.
2. Manufacturing
- Raw Material: Turbine blades are manufactured from nickel-based superalloys, which contain elements such as Cr, Co, Mo, W, Ta, Re, Nb, Al, and others, providing high heat and corrosion resistance.
- Investment Casting: Due to their complex shapes, turbine blades are created using the investment casting process. This involves mould making, wax pattern production, investment, and de-waxing. Investment casting ensures high accuracy with minimal need for secondary machining.
- Machining:
- Grinding: Grinding of nickel-based alloys is challenging due to thermal damage and formation of white layers. Technologies like BLOHM PROKOS high-speed reciprocating grinding help mitigate these issues.
- Drilling: Electrical Discharge Machining (EDM) and laser drilling are used to create precise holes and improve cooling efficiency in turbine blades.
- Deburring: Burrs from machining processes are removed using brush processes or abrasive substances to ensure smooth surfaces.
- Finishing: Post-machining processes include vapour degreasing and plating. Vapour degreasing ensures clean surfaces, while plating, such as platinum aluminide coating, provides oxidation and corrosion resistance.
3. Operation
- Usage: Once manufactured, turbine blades are installed in jet engines where they operate under high-temperature and high-pressure conditions. They extract energy from the gas produced by the combustor and drive the engine’s compressor and propeller.
4. End-of-Life
- Decommissioning: At the end of their operational life, turbine blades must be decommissioned. This can occur due to age, wear, or damage.
- Dismantling: Turbine blades are removed from the engine and evaluated. Components that are still in good condition may be repaired and reused or sold as spare parts.
- Recycling:
- Material Recovery: Materials like nickel from turbine blades can be recycled using closed-loop processes. For example, nickel can be combined with carbon steel scrap to produce stainless steel, reducing the need for primary nickel production.
- Recycling Methods: Turbine blades are subjected to recycling processes such as melting and remanufacturing. This reduces energy consumption compared to primary production and minimizes waste.
- Component Management: Components that cannot be reused in their original form are dismantled further, and a valuation is performed for potential reuse in non-aerospace markets. Non-recyclable materials may be disposed of in landfills or used for energy recovery.
5. Recycling and Sustainability
- Economic and Environmental Benefits: Recycling turbine blades contributes to economic savings by reducing the need for raw materials and minimizing disposal costs. It also offers significant environmental benefits by conserving resources, reducing energy consumption, and lowering landfill use.
- Sustainability Framework: Effective management of turbine blade end-of-life involves a systematic approach to recycling, adhering to sustainability criteria, and developing models to improve recycling practices.
Veeramanikandan, R.; Nithish, S.; Sivaraj, G.; Vinodh, S. (2017). Life cycle assessment of an aircraft component: a case study. International Journal of Industrial and Systems Engineering, 27(4), 485–. doi:10.1504/ijise.2017.087835
https://www.diva-portal.org/smash/get/diva2:1766557/FULLTEXT01.pdf
I WANT TO SELL
Do you have any spare parts for gas turbines you want to sell? Please Inquire now through our online submission form or contact us via phone, to assess the value of your as-removed parts.